The Basics of Rubber Combustion
The flammability of a rubber compound is a deciding factor in determining whether it is right for any given application. Rubber fabricators must have a working understanding of polymer flammability to maintain optimal safety and efficiency. This also requires us to have a thorough understanding of combustion.
There are three necessary components for combustion, as evident in the Fire Triangle model. The three parts include oxygen, fuel, and an ignition source. This essential principle is that you can prevent or extinguish a fire by eliminating one of the three elements. This is not only useful for stopping combustion as it occurs, but it also helps manufacturers understand how they can adapt polymers to be less flammable.
Different polymers undergo the process of combustion in different ways. The widely accepted general process includes a sequence of thermal and chemical changes, decomposition of a polymer, ignition of gases, combustion, and spread of a flame.
First, the source of ignition leads the plastic to rise in a temperature specific to that plastic’s chemical structure. Next, this plastic starts to break down, which forms free radicals and causes the gases to surround the bulk material, ignite, and begin combustion. Once enough energy accumulates, the burning of gas starts combustion at the plastic surface. Finally, the process results in flames and any combination of charring, smoke, and gases.
Testing for Polymer Flammability
The materials we use in custom rubber parts manufacturing need to be safe for each and every application. Polymer industry professionals use a range of tests to measure flammability levels when developing plastic and rubber materials. These tests include:
- Limiting Oxygen Index (LOI)
- This test determines the level of oxygen necessary to yield the combustion of a substance. An LOI test involves the placement of a plastic sample into a glass column. The sample acts as a wick as a flame ignites it, then the substance burns down. Once the previous step is complete, a researcher records the oxygen and nitrogen levels, which are unique to all plastic types.
- Vertical Burning Test (94V)
- For this test, one burns a candle-like sample plastic piece from the bottom up. The substance then gets a classification in accordance with the duration of flame after placement.
- Horizontal Burning Test (94HB)
- The Horizontal Burning test involves the placement of a flame at one end of a horizontal plastic sample. Next, the flame makes contact for 30 seconds or until it reaches a certain mark on the sample piece. A plastic material then gets a classification for the time required to reach the determined mark.
The results of these tests will determine whether a material is safe for the production of certain products. If a polymer is too flammable, rubber fabricators can reduce the flammability with certain additives in the hopes of creating a more viable material.
Which Rubber Compound is Best for the Job?
Choosing the ideal rubber materials for your project requires more than just an understanding of polymer flammability. If you want the highest quality and performance out of your rubber parts, you need to know the ins and outs of each rubber compound. Some factors to consider when choosing a rubber compound include:
- Your Industry
- Design Specifications
- Environmental Conditions
- Operating Temperature Range
- Resistances: UV, Chemicals, etc.
- Component Installation
Getting this information together is a great start to the selection process, but many compounds have overlapping properties and advantages. How do you choose the best compound under these conditions?
Let’s say you choose EPDM, a durable and versatile rubber with resistance to UV, ozone, weathering, aging, and various chemicals. If you are planning on using this for roofing, HVAC, automotive, or industrial applications, it may be the right choice. However, if your application will expose the rubber to oils and fuels, the parts you use will break down quickly and become unusable.
With Qualiform Rubber Molding, you do not have to go through all this confusion to choose the rubber compounds you need. We have a full selection of high-quality rubber compounds, so we can meet the requirements of any industry. Our staff will give your expert recommendations depending on your application environment, ensuring your components will work properly after installation. Check out our resources page for more information on rubber compounds.
Why Choose Qualiform for Your Custom Rubber Parts?
When you choose Qualiform, you work with rubber molding experts that have supplied clients in several industries with the components they need. In fact, we are an ISO 9001:2015 certified manufacturer offering injection molding, compression molding, transfer molding, extrusion, and rubber-to-metal bonding services. This is why automotive, medical, and even aerospace organizations depend on us for their custom rubber parts.
We have been in the rubber molding industry for over 50 years. Our staff combines countless years of industry experience with state-of-the-art equipment to develop the highest quality rubber component solutions on the market. We never say no to a challenge, and we have no problem meeting even the strictest quality and performance standards.
Qualiform also offers the quickest production and shipment for projects of nearly any volume. We operate on a 3-shift/24-hour schedule, which allows us to offer the fastest turnaround while maintaining affordable pricing. Choosing Qualiform means you always receive the parts you need exactly when you need them.
Are you looking for a rubber parts manufacturer but are unsure of what you need? Get in contact with Qualiform today, and our technical staff will be happy to answer your questions and get you started on your next project!
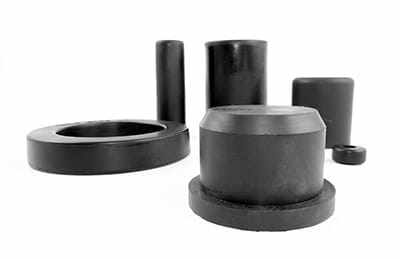