Rubber Injection Molding
The Custom Rubber Injection Molding Experts
With over thirty years of experience in rubber injection molding, Qualiform offers competitive pricing paired with unmatched product quality and service. As a leading provider of rubber injection molding to OEMs across the US, Qualiform Rubber Molding is trusted for our expertise in material properties, rubber compound selection, design consultation, and complex part molding.
Certified to ISO 9001:2015, Qualiform is experienced in meeting the strictest quality standards, ensuring that our products and services consistently exceed expectations. OEMs nationwide rely on our commitment to excellence and precision in every project.
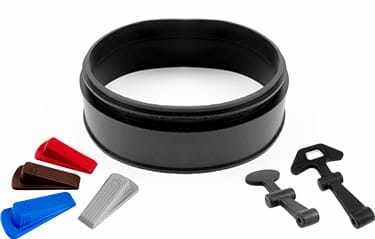
Our technical staff is ready to assist you with all your custom rubber injection molding needs.
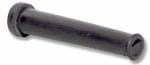
An example of a flexible strain relief protector.
Rubber Injection Molding
Rubber injection molding is used to develop both solid rubber parts and rubber-to-metal bonded products. Natural and synthetic rubber compounds can provide a wide variety of properties that solve problems from seals or gaskets, noise and vibration isolation, abrasion and impact resistance, and chemical/corrosion resistance. Rubber injection molding is ideally suited for mid-to-high-volume production and where tight tolerances, part consistency, or over-molding are required. In addition, rubber injection molding works well with rubber compounds that have faster cure times. This is a process that can be fully automated.
The Rubber Injection Molding Process
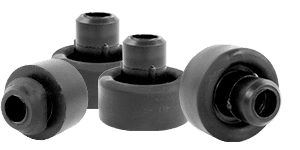
Vibration isolation grommets customized for your needs.

Specific customized rubber grommets for your needs.
Injection Molding Advantages
- A mid-to-high volume, efficient process
- Full automation is available
- Provides high-tolerance, precision rubber molded products
- The best rubber process for consistency and repeatability
- Allows for molding of complex geometry
- Ideal for rubber to metal bonding, insert molding and over-molding
- Color molded rubber
- Lower unit cost
- Eliminates preforms and preform labor cost
- Flashless molding / flashless tooling / eliminating secondary trimming
- Rapid cavity filling
- Reduced cycle time
- Minimal material waste
Injection Molding Disadvantages
- Higher start-up/shutdown costs
- Suited for high volume applications
- Not all elastomers are suitable due to fast cure times
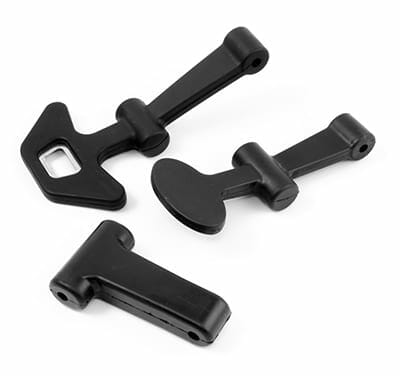
Typical Parts Produced with Rubber Injection Molding
- Rubber boots
- Rubber gaskets
- Rubber seals
- Rubber grommets
- Colored rubber products
- Rubber bumpers
- Rubber grips
- Rubber diaphragms
- Rubber bellows
- Rubber shock absorbers
- Rubber to metal bonding products
- Complex rubber products
- Vibration control parts / vibration isolation parts
- Chemical or corrosion resistant parts
- Abrasion-resistant parts
- Custom rubber parts
Materials We Process
- Butyl
- SBR
- Natural Rubber
- Silicone
- Colored Compounds
- EPDM
- Nitrile
- Viton©
- Neoprene
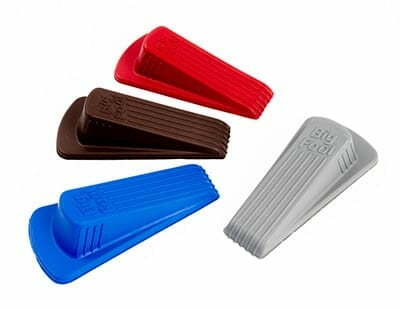
Rubber Molding Capabilities
Different molding processes have different strengths. That’s why Qualiform offers quality custom rubber compression molding, custom transfer molding, custom rubber injection molding, and rubber to metal bonding. Our experts help you match the best process to your project.
Why Qualiform For Your Rubber Injection Molding?
With unparalleled experience, Qualiform is the top U.S. rubber molder for custom rubber products. At Qualiform, we know that quality custom rubber products often require special compounds and present unique design and molding challenges. Our team of problem-solving, experts is well-equipped to handle all aspects of rubber molding and rubber to metal bonding with the utmost regards to their customers.
As the leading supplier of rubber molding services, compression molding, transfer molding, rubber to metal bonding, and rubber injection molding, we at Qualiform understand the importance of a fast turnaround. We are committed to running a 3-shift, 24-hour production facility for the quickest possible turnaround.
Rubber Molding Company Certifications
As a certified ISO 9001 company, we are dedicated to producing high-quality custom rubber molded products while taking the necessary steps to understand your project needs and ensure that they meet your full satisfaction. Qualiform is committed to implementing an effective quality assurance program that oversees, evaluates, and documents every aspect of our process, assuring top-notch quality with every product and service that we provide to our customers.
Competitive Pricing
Qualiform is committed to our customers, our environment, and our country. The competitive pricing that Qualiform offers our customers is a result of evaluating every aspect required to produce the part. Through research and development, our team at Qualiform analyzes the entire project scope to provide our customers with the best solution at the best price.
Green initiatives are taken by using repurposed rubber as often as we can. In turn, we are able to reduce costs and limit the amount of waste going into landfills.
As an American-owned company that works solely with American-Made products, Qualiform sources all of our tooling from within the United States. This allows faster lead times and faster responses to customer design changes.
Types of Rubber Products We Manufacture
Rubber Injection Molding FAQ’s
Our Capabilities
Qualiform has the experience and the knowledge to complete your custom rubber molding project needs. In business since 1976, Qualiform has built its enviable reputation on superior quality and a solid commitment to customer service. Our offerings include rubber compression molding, rubber transfer molding, and rubber injection molding. In addition, we have an extensive line of services, such as color compounds and rubber to metal bonding. Our range of capabilities means we are positioned to provide the custom molded rubber products you require.
From Design through Inspection
From start to finish, Qualiform will produce your design with top-notch customer service. We create quality custom transfer molding, rubber to metal bonding, custom injection molding, and rubber compression molding. We have the ability to complete jobs other manufacturers would fall short in, due to our extensive manufacturing capabilities.
Our Specialties
Our services include custom rubber transfer molding, custom rubber injection molding, rubber to metal bonding, rubber parts manufacturer, custom rubber molding, custom rubber compression molding, rubber parts manufacturer, rubber products manufacturer.
Additional Questions
Our technical staff is available to answer any questions you may have. Qualiform customer service support provides reliable, courteous, and responsible communication that includes a detail-oriented follow-up with every customer.
Call us at (330) 336-6777 or submit an inquiry through our contact form.