The Leaders in Rubber Extrusion
Qualiform is a premier provider of extruded rubber products in the industry. We employ an advanced and precise rubber extrusion process, ensuring that every customer receives the optimal product for their application. As a leading rubber extrusion manufacturer, we can develop custom dies for each customer’s unique design. Our rubber extrusion process offers several advantages:
- Ability to create various unique shapes
- Efficient and cost-effective production
- Lightweight, durable products
- Low waste production
What is Rubber Extrusion & How Does It Work?
The extrusion process creates objects based on a desired cross-sectional profile. We manufacture extruded rubber parts with soft, unvulcanized rubber materials. The extrusion process makes these materials even more soft and flexible, so we need to vulcanize the extruded product to harden it prior to application.
The rubber extrusion process begins with feeding unvulcanized rubber into an extruder, which feeds the materials into a hopper. The hopper then pushes the rubber through a variety of flutes in a revolving screw. The screw then forces the rubber through a die of the desired cross-section under pressure and temperature that increases as the material approaches the die.
Upon reaching the extrusion die, the pressure will force the material through the die’s openings. As a result, the material will swell depending on the specific rubber compound’s innate hardness and other characteristics. This swelling also means the components will require plus or minus tolerances on cross-sections.
Qualiform is one of America’s leading rubber extrusion companies. We have optimized this process for faster production, minimal waste production, and reduced costs, so you get the parts you need, when you need them, at a price you can afford.
Strengthening Rubber Through Vulcanization
Post-processing of rubber extruded products involves vulcanization of the materials. We cure the rubber with sulfur and other curing agents. This causes the rubber to become far stronger, so it can operate properly in its application. We also perform other secondary processes such as cutting to size, splicing, drilling, end joining, and powder dusting to avoid any sticking.
Vulcanization often causes shrinkage and swelling in the rubber components, which varies depending on the type of rubber materials involved. Once we finish the vulcanization process, the extruded part will typically reduce in size in the center more than at its ends. If you are not sure you fully understand this process, do not worry. Our staff will be available to assist you at each stage of production.
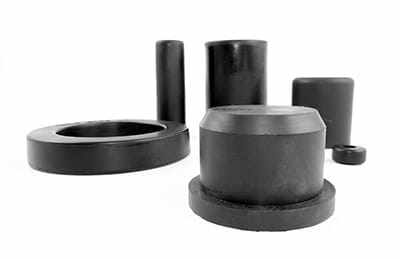
What Can We Make with the Rubber Extrusion Process?
Rubber Gaskets & Seals
Our custom gasket and seals are ideal for a wide variety of sealing applications. Extruded gaskets are a specific type of seal designed to fill the space between two connected parts or areas. Some of our standard sealing extrusions include EPDM rubber seals, extruded rubber tubing, flare trim, locking gaskets, rubber edge trim, and o-ring cords. We can produce these in square and cord configurations as well as countless custom hollow shapes.
Here at Qualiform, we take all factors into consideration when designing our rubber gaskets and seals. Our sealing components offer high-level performance in even the toughest applications. We will help you determine the ideal rubber compounds and sealing designs based on your industry’s environmental conditions.

Rubber Window Glazing
Extruded rubber window glazing is a type of seal that prevents air, water, and other fluids or gases from leaking through windows. You may also see these seals referred to as weather stripping, glazing strips, or glazing gaskets. The most common application for window glazing is for reducing energy consumption in residential and commercial properties. These seals are perfect for keeping the heat or A/C in, so you can lower your gas and electric bills.
Some other applications for window glazing include car doors, windshields, airplane window seals, sunroofs, boat hatches, and more! However, not all window glazing has the same design requirements. Qualiform offers more than 50 years of experience in developing these seals, so we can determine the ideal profile shapes and rubber materials for your application.

Custom Extruded Rubber Profiles
One of the biggest advantages of the rubber extrusion process is customizability. Rubber extrusions can come in numerous different shapes, sizes, and configurations with each type offering a unique set of uses and benefits. While rubber extrusions are most often used for sealing, they are also used for vibration control, impact absorption, noise cancellation, and even as a decorative addition to your home’s windows.
Our experience with the rubber extrusion process allows us to produce a wide range of extruded rubber profiles. With high-precision equipment, we can create the perfect rubber profile for nearly any project. Check out our selection of extruded rubber profiles to learn more.

What Industries Use Rubber Extrusions?
Qualiform has supplied a diverse range of industries with high-quality extrusions for many years. Industries including automotive, aerospace, marine, medical, food processing, and more depend on the sealing and impact absorption properties of rubber extrusions.
There are already countless rubber extrusions in your home! The majority of modern home appliances use some form of rubber extrusion for countless reasons. Even a pencil eraser is a rubber extrusion!
Once you leave the home, you will run into even more rubber extrusions. Your car and your bike both utilize several of these parts to function properly. More advanced applications include submarines and even space shuttles. For warehouses and factories, extrusions come in the form of rollers, sheets, and rods to absorb the loud noises and intense vibrations coming from heavy machinery.
Regardless of your industry, Qualiform can develop products to meet your unique quality and performance requirements. The industries we serve depend on our rubber extrusion process to deliver the highest quality products on the market.
Are you looking for rubber extrusions or other custom rubber products? You can depend on Qualiform Rubber Molding. We are a leading provider of custom rubber molding solutions, and we are fully certified to ISO 9001:2015. Our staff consists of experts in all things rubber molding including injection molding, compression molding, transfer molding, rubber-to-metal bonding, and more!
Not sure of what process you need or what product you are looking for? No problem! Our technical staff will be happy to answer your questions. We will provide you with professional recommendations and point you in the right direction, so contact Qualiform today to get started on your project!
