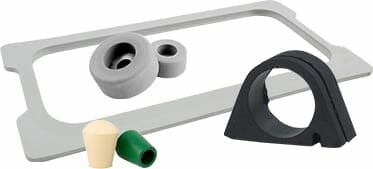
Rubber Transfer Molding
The rubber transfer molding process is ideal for manufacturing solid rubber components, rubber parts with inserts, and products that need to bond rubber to metal. It merges the advantages of injection molding with the straightforwardness of compression molding. This technique is especially effective for producing rubber items that demand:
- Exact positioning
- Bonding rubber to fragile metal parts – such as wire
- Mold designs that contain multiple cavities and can trap air
- Intricate parts with lower volume requirements
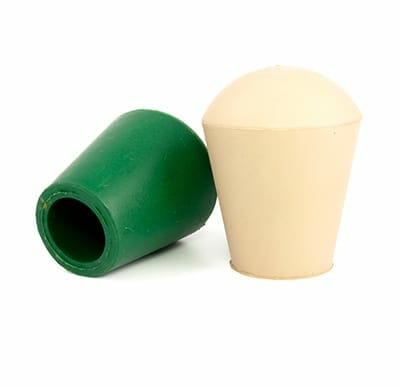
Neoprene transfer molded eye protection product used on top of antenna.
Qualiform’s Rubber Transfer Molding Process
Our process of transfer molding involves pushing unvulcanized rubber through sprues into a heated mold. Similar to compression molding, transfer molding requires raw material preparation into pellets and/or pre-forms.
Rather than placing the preform in the mold cavity, the rubber pre-form is placed in a chamber “pot” at the top of the mold then placed in a press. In the pot, the material is compressed by a heated plunger and transferred through sprues into the cavity below. During this, the plunger is kept in place until the preform takes on the shape of the mold and the rubber is vulcanized. Once the part cures, hardens, cools, it is then ejected. Any excess cured rubber left in the pot is removed and the mold cavities are cleaned for the next molding cycle to begin.
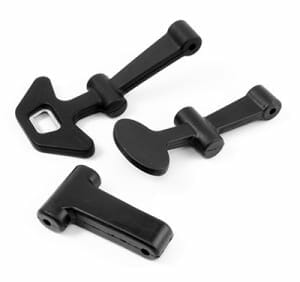
Transfer molded EPDM latches.
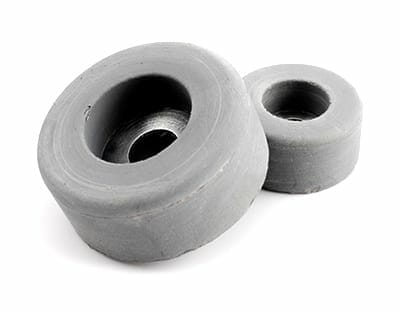
Feet for application use on bottom of Red Box DVD machines.
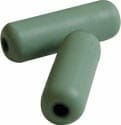
Custom dental grips with numerous color options available.
Transfer Molding for Rubber to Metal Bonding
Transfer molding is an important part of the rubber to metal bonding process or over molding, the components are loaded into a heated mold either by hand or using a loading fixture. Material is then loaded into the well pot of the transfer mold. Once the mold closes, the rubber is heated and then transferred through the runner. The gate sprues into the mold cavities and around the metal insert. With the pressure and elevated temperatures, the rubber cures and vulcanizes, allowing the parts to be removed.
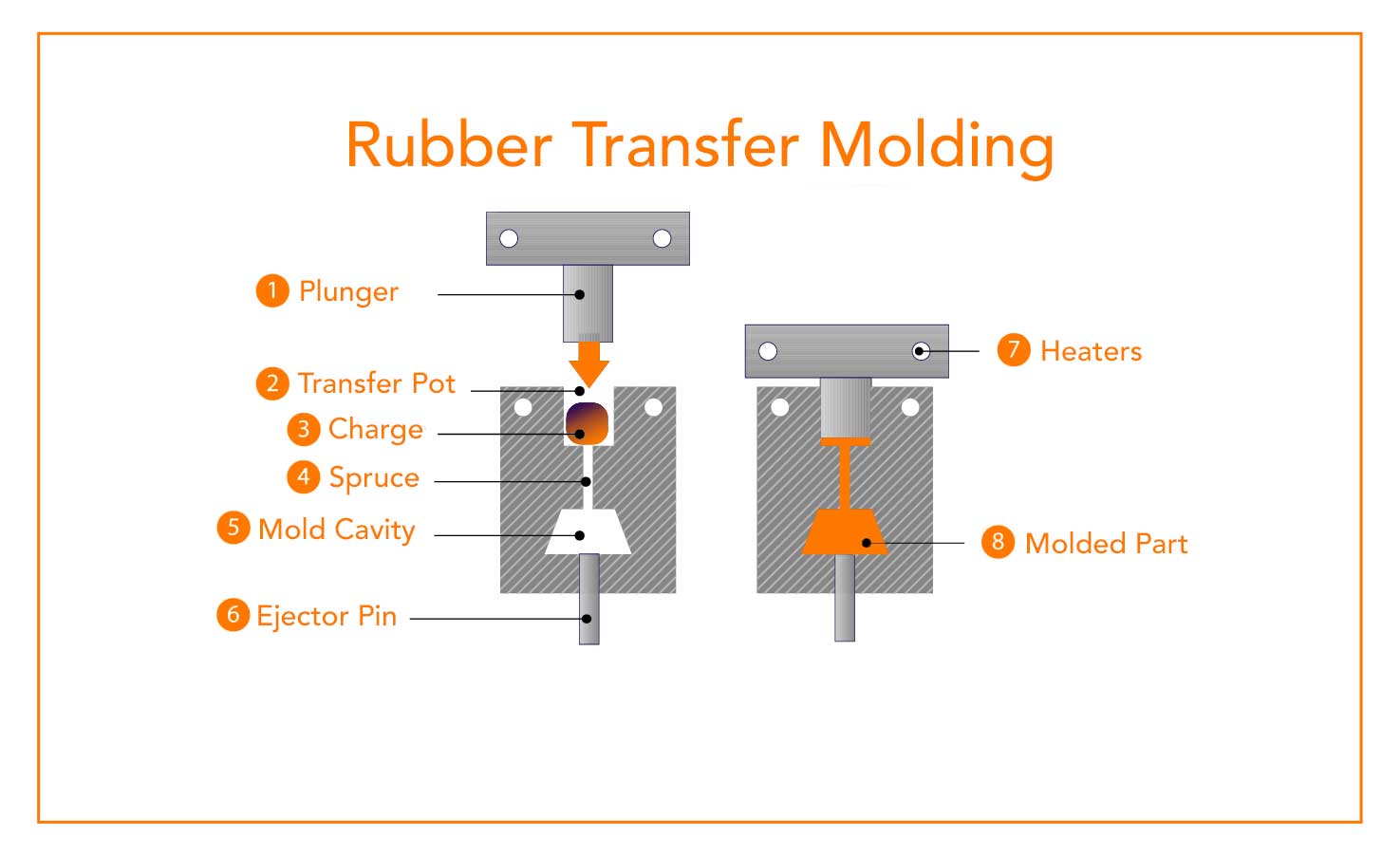
The rubber transfer mold consists of a piston, well pot, sprue plate, cavity plate, and a base plate with a knock-out system used to eject the parts after molding.
Certified Rubber Molding Company
Qualiform is a certified ISO 9001:2015 company. We provide our customers with excellent service and the highest quality custom rubber-molded products, to ensure all of their specific needs are met. Contact Qualiform Rubber Molding if you are in need of any assistance with product development. Our expertise includes a variety of molding services including, injection molding, compression molding, transfer molding, and rubber-to-metal bonding.
Our expert staff will be available to assist you throughout the entire design and development process. We will work diligently to ensure each product meets your needs and specifications. At each step of your product’s development, our staff will be by your side ensuring the materials and product quality are to your satisfaction.
Questions?
Our technical staff is available to answer any questions call (330) 336-6777, or submit a question through our Contact Form or Send Us a PDF.