Factors Affecting Tolerances in Molded Rubber Parts
Factors Affecting Rubber Tolerances:
Mold Design / Inserts / Trim and Finish / Distortion / Shrinkage / Storage Conditions / Dimensions
All of Qualiform’s rubber molding processes take place right here in the U.S.A. All our rubber molded products are American-made and designed to your unique specifications. Qualiform Rubber Molding delivers fast, reliable manufacturing of high-quality rubber products and rubber compound development at a competitive price. The tolerances of molded rubber products can be affected in a number of ways during the manufacturing process.
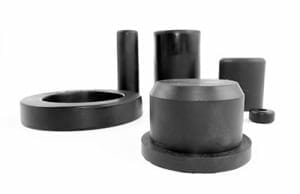
Mold Design
One factor affecting tolerances of molded products is mold design. With any type of mold, all molds will require some tolerances causing some cavities to display variances from others. This is why it is essential for the dimensional tolerances on the rubber product to allow for these slight variances. The accuracy of the mold register, or the various plates of the mold that come together to form the mold cavity, should also be considered. For molds requiring high precision in dimensions and register, the design work and machining must be more precise and the cost of the molds will be greater than one with commercial requirements.
Regardless of your precision requirements, our tooling design will always attempt to yield the highest precision and longest mold life that the price of the mold will allow. When you choose Qualiform, we will work with your tooling from other molders, or we can purchase new tooling for you. As a Qualiform customer, you always own the tooling. We work to keep you as a customer through unparalleled customer service.
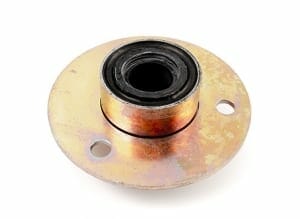
Inserts
Insert materials including metals, fabrics, plastics, etc. often have their own standards for tolerances. However, in designing molded rubber products that have inserts, other factors should be considered. These factors include:
- How the inserts fit in the mold cavities
- Proper hold spacing to match the inserts with mold pins
- Location of the inserts with respect to other dimensions
- The fact that inserts at room temperature must fit into a heated mold
Qualiform Rubber Molding is an ISO 9001:2015, and we are dedicated to employing the most effective quality assurance program. This program oversees, evaluates, and documents every aspect of our molding processes so we can continue to comply with customer requirements and ensure satisfaction with each product and service we offer.
Trim and Finish
As with cut parts, secondary operations, such as flash removal, can result in dimensional variation in the finished part and is a factor affecting rubber tolerances. Trimming and finishing operations work to remove excess rubber material that is not part of the finished product, such as flash. This process is often successfully completed without affecting important dimensions; in some instances, however, material can be removed from critical areas of the part itself. This can occur in tumbling, where the process may wear down the finished and exposed surface of the molded rubber parts.
Qualiform is committed to pursuing the best technology and resources available in the industry to design, engineer and manufacture superior rubber molded products that exceed all customer requirements for quality and service. Mechanical trimming may be able to control dimensions in rubber parts with thin lips or projections in the mold parting line. Qualiform’s knowledgeable staff can help customers choose the right process, materials, and mold design for their rubber molded products.
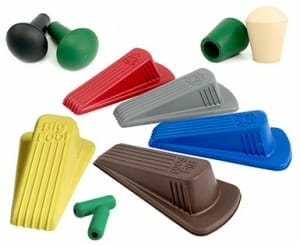
Distortion
Because rubber is flexible material, its shape can be affected by temperature. Distortion can occur when the part is removed from the mold or when it is packed for shipment. It is possible for distortion to occur when the rubber part is removed from the mold through the process of stretching it over a core. Distortion can present difficulties in the measurements of rubber parts and should therefore be minimized through the practice of storing the rubber part in an unstressed state for 24 hours at room temperature after it has been molded. Some rubber will crystallize (stiffen) when stored at low temperature and must be heated to above room temperature to overcome this condition.
Developing the best custom rubber components for your applications requires using only the finest rubber materials. Qualiform has the ability to process a variety of high-performance polymers depending on your application. Qualiform has the necessary knowledge and experience to analyze your project and offer accurate material recommendations.
Shrinkage
All rubber materials exhibit some amount of shrinkage after molding when the part cools. In molding rubber parts, there may be difference between the mold dimensions and the completed part. While the amount of shrinkage can be minimized, it cannot be eliminated entirely. The mold designer and the compounded must determine the amount of shrinkage for the selected compound and incorporate this allowance into the mold cavity size.
Even though the mold is built to anticipate shrinkage, there remains an inherent variability that must be covered by adequate dimensional tolerance. Shrinkage of rubber is a volume effect. Complex shapes in the molded product or the presence of inserts may restrict the lineal shrinkage in one direction and increase it in another.
Qualiform’s knowledgeable staff work closely with customers and our raw material suppliers to develop rubber compound to best meet the required properties of the end product. A wide range of rubber compounds, additives and fibers can produce virtually and product characteristics from abrasion resistance, chemical resistance, corrosion resistant, heat resistant, ozone resistant, and vibration isolation to impact absorption. Rubber compounds can be modified to produce the exact material properties required including rigidity, durability, strength and flexibility.
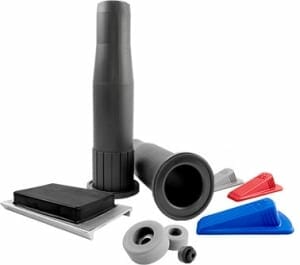
Environmental and Storage Conditions
One of the biggest factors affecting rubber tolerances is evironmental and storage conditions. Rubber changes in dimensions as temperature and humidity changes. For molded parts that are used in critical applications that require precise dimensioning, the temperature and humidity under which a part is to be measured should be specified.
Humidity — Some rubber materials will absorb moisture. Depending on the material used in the molded rubber, some parts will exhibit changes in dimensions based on the amount of moisture present in the rubber product. In molded products that will exhibit these properties, tolerance for moisture expansion or contraction must be included in the dimensions. The effect of humidity on a rubber product can be minimized through stabilizing the product in an area where the humidity is controlled for a period no less than 24 hours.
Temperature — As already discussed, changes in temperature will often cause changes in the dimensions of rubber materials. Different compounds will carry with them different coefficients of expansion based on environmental exposure to temperature. In rubber products that require critical or precise dimensions, the temperatures at which the rubber parts will be used should be measured and the time required to stabilize the part at said temperature should also be specified.
Dimension Terminology
Fixed Dimensions — Are parallel to the mold parting line or the parting lines of major mold sections and are those dimensions that are not affected by flash thickness variation.
- Example – A Sample wheel, with half of the wheel formed in each half of the mold and the flash line located around the O.D.
- The fixed dimensions are the OD and the hub diameter
Closure Dimensions — Are vertical to the mold parting line or to the parting lines of the major mold sections and are those dimensions that are affected by flash thickness variation.
Closure dimensions will be affected by a number of factors additional to those listed above including, weight and shape of raw material stock, flow characteristics of that stock, and types of flash grooves or other relief devices in the mold. These variables will all affect the final degree of mold closure.
Although affected by variations in flash thickness, closure dimensions are not always related to basic flash thickness. In manufacturing processes that include machine or die trimming a molded rubber product, the mold itself will be designed with a thicker artificial flash than rubber parts that are designed for hand deflashing or tumbling. Thus, although the same rubber part from two different sources may meet drawing dimensions, they may also exhibit a difference in basic flash thickness at the parting line depending on the molding process and deflashing method employed.
Most molded rubber parts will have a logical place for the mold designer to locate the parting line that allows for the soundest control of dimensions.
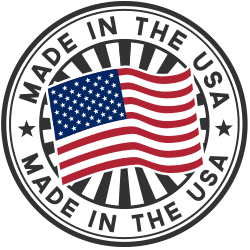
Qualiform Quality Assurance
Throughout the entire design and development process, our expert staff will be by your side to assist you. With over thirty years of experience, we can ensure each product meets your needs and specifications. Our staff will work with you at each step of your product’s development, ensuring the materials and product quality are to your liking.
Qualiform is a leader among U.S. rubber molding companies. We are a top molder of custom products requiring special compounds or unique designs. Our experts have immense experience in all aspects of rubber molding and offer an incomparable ability in problem-solving, allowing us to work with products that present specific molding challenges like these factors affecting rubber tolerances.
Our Customer Servicer Support provides Qualiform customers with courteous and reliable communication. We also include detail-oriented follow-ups with each customer, ensuring they are aware of the inner workings of each step of the process.