Rubber Extrusion Company
Qualiform is a Leader in Rubber Extrusion Manufacturing Companies
If you’re looking for top rubber extrusion companies, look no further than Qualiform. We specialize in providing high-quality custom rubber extrusions from premium materials, including SBR, Butyl, Colored Extrusions, EPDM, Neoprene, Viton™, Nitrile, Fiber Forcified Rubber, and Natural Rubber. Our extruded rubber profiles are fully customizable to meet your specific needs, whether for rubber gaskets and seals, hose, tubing, cord, or complex configurations. Trust Qualiform for exceptional performance and precision in all your rubber extrusion projects.
Applications for Custom Extruded Rubber
Our custom rubber extrusions are used across a wide range of industries including automotive, marine, aerospace, manufacturing, healthcare, transportation, electronics, and food processing. No matter what the application, you can rely on Qualiform for expert technical support and material recommendations, high-quality products, dependable delivery, and outstanding customer service.
With more than 50 years of rubber manufacturing experience, Qualiform leads the other rubber extrusion companies. We take the time to understand your specific application and recommend the best materials, for the environment in the rubber extrusion will be used. Our technical experts are available to consult on the ideal extrusion profile design for the application. We can make recommendations regarding the best sealing, insulating, impact or sound absorption, wear resistance, and other characteristics that will impact the performance of the extrusion.
Rubber extruders make a wide range of shapes and products that are invaluable in everyday home life, such as rubber trim, weather-stripping, extruded rubber seals, rubber floor matting, rubber grommets, connectors, bumpers, and more. In general, rubber extrusions are valued as sealants and gaskets because they offer such excellent flexibility, impermeability, and resilience. They even make up the eraser on the end of a pencil. Outside of the home, rubber extrusions are used in cars, on bicycles, on space shuttles, and on submarines. In warehouses and manufacturing facilities, rubber rollers, sheets, and rods absorb the noise and vibration caused by moving machinery.
Rubber Window Glazing Profiles
Qualiform is a leading provider of rubber extrusion services, offering a full range of rubber window glazing seals for a wide variety of industries. As a certified manufacturer of custom rubber products, we utilize advanced rubber molding technologies to ensure high-level precision for every project. So, we can reliably produce the ideal rubber window seal extrusions for your application.
Rubber window glazing seals are specially designed to keep air, water, and other fluids from leaking in or out of the window. These are most commonly found in residential and commercial properties as a means of minimizing energy consumption, but can also be found in the automotive and marine industry.
Rubber Extruded Seals and Gaskets
Sealing rubber extrusions and extruded rubber gaskets are used across a wide variety of applications. Applications include EPDM rubber seals, extruded rubber tubing, o-ring cord, flare trim, locking gaskets, rubber edge trim, and trim seals. They can be provided as squares, cords, or custom hollow shapes. Qualiform can recommend the best rubber or engineered synthetic compound for compression sealing based on the intended use.
Qualiform’s experts consider both factors in the design stage of rubber gaskets, so they will not be the weakest link in a product. Similarly, they consider environmental factors in the gasket or rubber seal application. Qualiform’s highly experienced team can easily assist you with your custom rubber gasket or seal project. Our experienced technical staff considers many factors in the design process, so they can recommend the best method to meet your quality and cost requirements.
The Rubber Extrusion Process
As a rubber extrusion company, we develop a custom extrusion die based on your required design. Unvulcanized material is fed into a hopper. A rotating screw adds pressure, heat and pushes the material into the die. The high-pressure extrusion machine (extruder) then forces the rubber compound through the die. The die then forms your custom rubber profile shape. We stand behind the quality of all of our rubber beading profiles.
Rubber extrusions from Qualiform come in a wide range of shapes, sizes, and options. Each extruded rubber profile offers its own set of uses and advantages. Creating a seal is one of the more common applications of rubber extrusion profiles, but they can also be used for noise cancellation, impact absorption, vibration control, and even as decorative trim on windows.
Vulcanization of Rubber Extrusions
Post-processing of rubber extrusions involves the vulcanization process to strengthen the rubber. The rubber is cured with sulfur or other curing agents. Other secondary processes include cutting to size, drilling, splicing, end joining, and powder dusting to avoid sticking. Let Qualiform’s technical staff assist you in all steps of the process and demonstrate why Qualiform is the superior choice over other rubber extrusion companies.
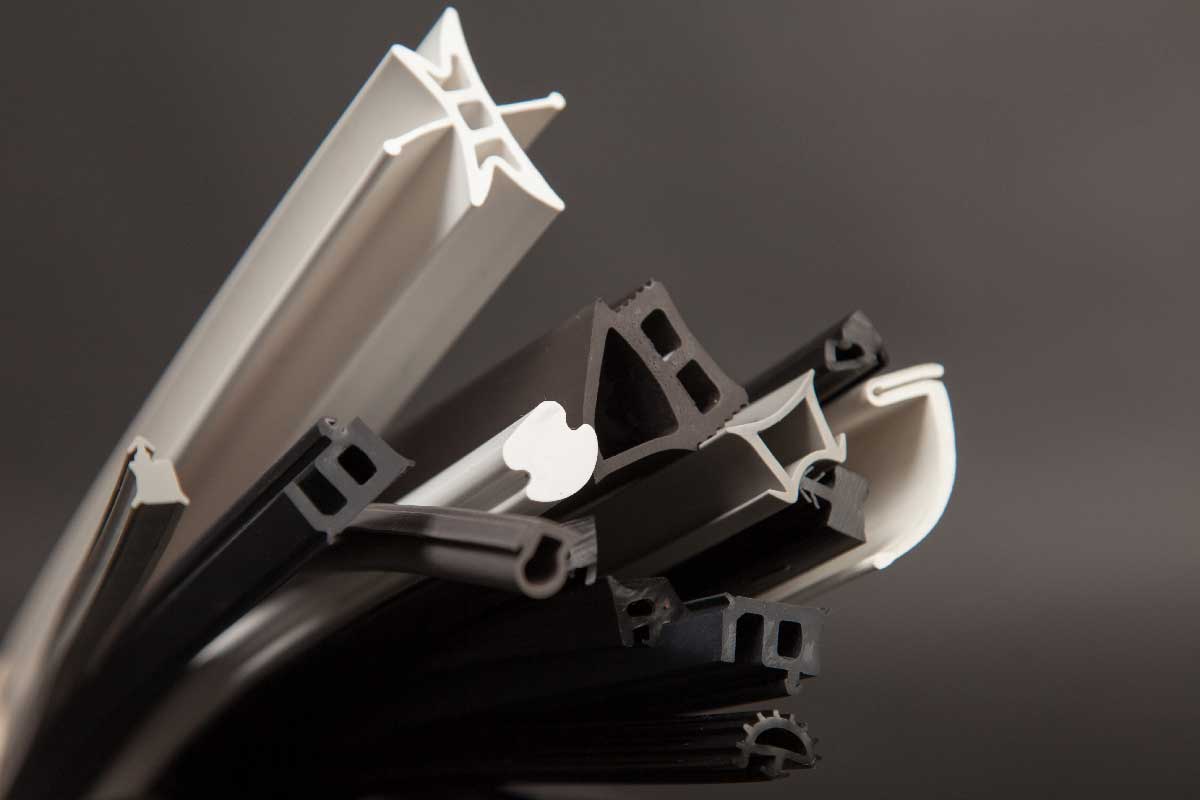
Applications
Glazing Rubber Seals We Produce
Materials Used in Rubber Extruded Products
To create a custom rubber extrusion, rubber extrusion companies think about a number of design factors, all related to the application. One of the first things considered is material. Rubber material choice depends entirely on how it will match the application requirements. Then, our rubber extrusion experts plan out the shape of the die. They may also consult their standard rubber die list, but they make new dies for a custom extrusion.
Based on the required properties and application of the finished extrusion, the rubber extrusion company, Qualiform can advise on the best material for the extrusion. Additional consideration will be given to any secondary processes that are required. Custom compounds and fiber integration can be used when needed.
Natural Rubber
Natural rubber provides excellent acid, chemical, and abrasion resistance.
Silicone Rubber
Silicone rubber is an FDA-certified elastomer that maintains its form and properties when exposed to both high and low temperatures.
Viton
Viton provides superior heat, chemical, and weathering resistance.
Nitrile
Nitrile, aka nitrile rubber, NBR (nitrile butadiene rubber), acrylonitrile-butadiene rubber, Perbunan, or Buna-Nis, is highly resistant to oils and ideal for O-rings, hoses, or hydraulic seals.
Neoprene
Neoprene has high tensile strength and resists heat, fire, UV rays, water, and oil.
Butyl
Butyl delivers low airflow permeability.
SBR
SBR (styrene-butadiene rubber) is used in applications that require high abrasion resistance.
EPDM
EPDM (ethylene propylene diene terpolymer) is ideal for applications that involve heat, aging, ozone, oxidation, and ultraviolet rays. Can be used for sponge rubber, foam rubber, weather-stripping, tarp straps, door gaskets, window gaskets, and roofing membrane.
Benefits of Choosing Qualiform for Rubber Extrusion Manufacturing
There are many reasons to choose rubber extrusion. First, it offers great freedom of design. You can request parts in nearly shape and size, and rubber extrusion companies can use nearly any rubber material. This means that you also have many choices when it comes to the qualities your part will exude. Another great benefit of a rubber extrusion is that it makes parts that are both strong and flexible and soft.