Rubber Compression Molding
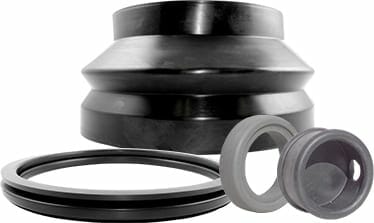
Our technical staff is ready to assist you with all your custom rubber compression molding needs.
The Rubber Compression Molding Process / Materials / Qualiform Compression Rubber Molding / Types of Rubber Products We Manufacture / Rubber Compression Molding FAQs
Rubber compression molding is an excellent choice for producing rubber components in low to medium volumes. This widely adopted and cost-effective technique is particularly well-suited for the creation of medium to large parts, especially in cases where high-cost materials and extreme hardness are required.
Rubber compression molding can produce a wide variety of custom rubber molded components, making it a cost-effective solution for creating large, intricate products. This process is frequently used to manufacture environmental seal products such as rubber O-rings, seals, and gaskets, ensuring high performance and durability.
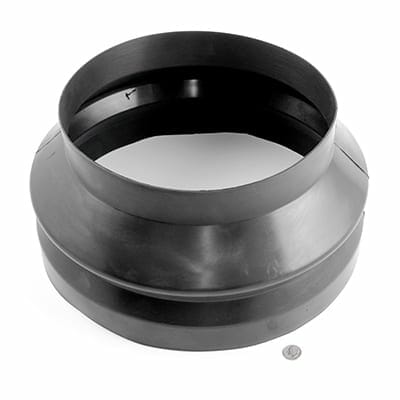
Viton rubber seal product.
The Rubber Compression Molding Process
The rubber compression molding process uses a preformed piece of uncured rubber that is placed in an open mold cavity. The mold is preheated to an elevated temperature. As the mold closes in the press, the material is compressed and flows to fill the rubber mold cavity.
The combination of elevated temperatures and high pressures activates the vulcanization process and curing of the rubber compound. Once an optimal cure is reached, the part hardens and cools then the mold is opened and the final part removed. The next rubber preform is inserted into the mold and the cycle repeats.
The basic compression mold is usually a two-piece construction consisting of a top and bottom plate. Half of the part cavity is usually cut into each plate of the mold. A trim area is created by grooves cut around each cavity which allows the excess rubber to flow out of the cavity. Compression molds are typically secured between heated press platens. The molded parts require trimming to remove the groove overflow. An additional bake cycle may be required for partially cured parts.
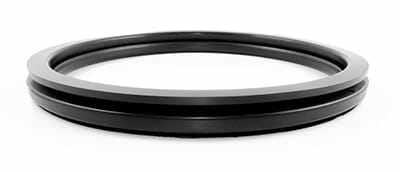
EPDM seal created for commercial washing machine use.
Advantages of Rubber Compression Molding
Rubber Compression Molding offers advantages over other methods by providing:
- Tooling savings
- Short setup time (saves on short production runs)
- The capacity to process stiff, high durometer materials
- Ideal for large parts that require a long cure time
- Maximized cavity count
- Ideal for low volume part requirements
- Ability to process most elastomers and cure systems
Disadvantages of Rubber Compression Molding
- Longer cycle times
- Mid-range precision and consistency
- Labor intensive
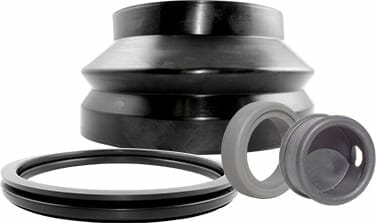
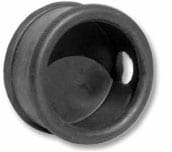
Compression molded air gauge guard.
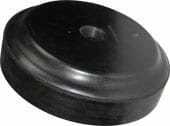
SBR natural rubber molded in a bumper for suspension application.
Qualiform Compression Molding
Qualiform Rubber Molding is a full-service rubber products manufacturer with more than 50 years of experience.
Depend on our rubber product manufacturing capabilities to meet the needs of the transportation, medical, electrical, plumbing, industrial, appliance, and aerospace industries.
We are here to serve all of your rubber molding needs!
Why should you choose Qualiform for Rubber Compression Molding?
– Trusted experience to solve your problems from design to price to delivery – try us!
– Short-runs with fast turnaround
– Competitive pricing on a variety of rubber parts
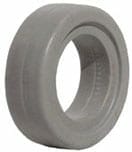
Rubber tires customized for hospital bed use.
– We work with your tooling either from other molders or can purchase new tooling for you. You always own the tooling so we keep you as a customer through outstanding performance and customer service.
– 3-shift/24-hour production for the quickest turnaround
– We aggressively monitor raw material costs to maintain the lowest possible pricing
– Green initiatives with repurposed rubber to reduce costs and save from landfills
– AMERICAN MADE PRODUCTS FROM AN AMERICAN OWNED COMPANY
Qualiform is the top U.S. rubber molder for custom rubber products that require special compounds and/or present unique design and molding challenges. We are experts when it comes to rubber molding services, compression molding, transfer molding, rubber to metal bonding and rubber injection molding.
Rubber Manufacturing Company Certifications
Certified to ISO 9001, we are dedicated to producing high-quality custom rubber molded products and will take the necessary steps to understand and ensure your project needs are satisfied. Please contact Qualiform for assistance with your rubber product development. Qualiform is the leading supplier of rubber molding services, compression molding, transfer molding, rubber to metal bonding, and rubber injection molding.
Our knowledgeable rubber compression molding staff will assist you with product development and design. Qualiform’s extensive rubber molding experience ensures we can meet your exact specifications. We work with you every step of the process to ensure the quality and materials meet your specifications.
Rubber Compression Molding FAQs
Our Molding Capabilities
Qualiform Custom Rubber Molding creates quality custom rubber compression molding, custom transfer molding, custom rubber injection molding, and rubber to metal bonding with the highest standards in customer service.
Qualiform Quality Assurance Program
Qualiform is an ISO 9001:2015 certified company, and is committed to endorsing an effective program that will be responsible for every aspect of our processes so as to comply with customer requirements. Qualiform will evaluate and document to assure satisfaction with every product and service we provide
Our Customer Service
Qualiform is proud of their Customer Service Support. Our customer support provides authentic disclosure with every customer we serve. This includes follow-up with every customer, informing them of each step of the process, with detail-oriented, customer-conscious professionalism.
Competitive Pricing on Rubber Compression Molding Products
Competitive pricing is the result of evaluating every aspect required to produce the part. Whether through R&D, design, engineering or manufacturing, Qualiform analyzes the entire project scope to determine the best solution at the best price.
Experienced Work Force
The Qualiform leadership team offers 150 years of combined knowledge and experience in all disciplines of the rubber mold industry. Qualiform employees are a valued asset. Qualiform pledges a continued dedication to investing in the expertise of our employees so as to maintain a status of quality performance and leadership within the ever-growing rubber industry.
Questions?
Our technical staff is available to answer any questions call (330) 336-6777, or submit a question through our Contact Form or Send Us a PDF.