Have you and your team been looking for custom rubber parts for your next project? Learn more about rubber processing details
Endless Possibilities for Customization | Rubber Processing Details
Without a doubt, not all rubber processing methods are ideal for every application. If you and your colleagues need custom rubber parts for your next project, then you will need to choose a rubber fabrication method that will help you get the most out of your project. Medical settings might require parts that are FDA approved while manufacturing facilities might benefit most from parts that can withstand harsh both conditions and high speeds, for example.
Overall, the key to successful customization is selecting the most cost-effective rubber fabrication method. When you connect with experts, you can benefit from a streamlined production process and quality parts, and even save on maintenance and repair costs in the long run.
Die Cut Rubber | Rubber Processing Details
The rubber die-cutting process involves the feeding of rubber sheets or strips into a machine, and the lowering of custom dies to cut the material into a custom shape. This is often the best fabrication method for thin materials, typically less than 0.25” thick or smaller. When fabricators try to cut material any thicker than this, it can result in dishing, which refers to a caving in of the finished rubber part.
This rubber fabrication method can effectively accommodate custom parts with squared angles and/or flat surfaces. Overall, the option is suitable for nearly any elastomeric material, and even mylar or cork.
Rubber Splicing | Rubber Processing Details
Splicing accommodates continuous loops in custom rubber extrusions. In all, it can provide an affordable alternative to rubber molding. First, fabricators extrude bulk rubber material.
Next, they leave the rubber material to cure, whether by autoclave, salt bath, or by microwave. Then, fabricators either splice the material by cold splicing or splice molding.
Cold splicing refers to the process by which fabricators bond two ends of a rubber extrusion with a rubber-compatible adhesive, while splice molding involves the bonding of two ends with both heat and pressure. Overall, splicing can accommodate most rubber materials and is ideal for hollow round gaskets.
Mandrel Formed Rubber Tubing | Rubber Processing Details
Mandrel forming starts with the extrusion of bulk rubber material. Next, fabricators cut the rubber to a specific length, and then “stick” the rubber onto a mandrel to shape the final part. After fabricators leave the rubber to cure, they transfer the pieces to cleaning equipment to get rid of any release agents or any excess material.
Mandrel forming is notable for its labor-intensive process. However, the method is ideal pieces that would otherwise kink with a bend, like hoses, for example. In all, mandrel forming accommodates most rubber materials.
Lathe Cut Rubber | Rubber Processing Details
Rubber fabrication by lathe cutting starts with the extrusion of a rubber tube. Next, fabricators cut this tube to the desired length. Then, this material goes onto a mandrel and then undergoes curing and grinding. Finally, fabricators cut for precision with a lathe.
Lathe cutting is especially effective for both precision rubber washers, hoses, lids and gaskets. Like die cutting, it accommodates the majority of elastomeric materials.
Rubber Punching | Rubber Processing Details
Punching can accommodate custom parts that require holes. Significantly, fabricators use a punch jig in what is essentially a modified form of die-cutting. Overall, the process can accommodate most rubber materials.
Rubber Splicing | Rubber Processing Details
Splicing accommodates continuous loops in custom rubber extrusions. In all, it can provide an affordable alternative to rubber molding. First, fabricators extrude bulk rubber material. Next, they leave the rubber material to cure, whether by autoclave, salt bath, or by microwave. Then, fabricators either splice the material by cold splicing or splice molding.
Cold splicing refers to the process by which fabricators bond two ends of a rubber extrusion with a rubber-compatible adhesive, while splice molding involves the bonding of two ends with both heat and pressure. Overall, splicing can accommodate most rubber materials and is ideal for hollow round gaskets.
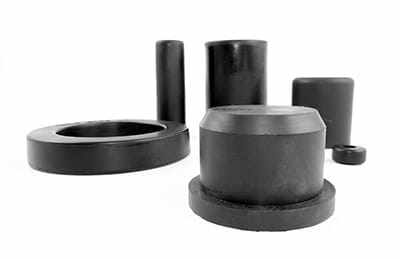