The Custom Rubber Gaskets and Seals Experts
Rubber Gaskets and Seals
Rubber gaskets and seals are essential for preventing moisture and air leaks in various applications. If you’re looking for gasket manufacturers near me, Qualiform is your trusted source for custom rubber gaskets near me and high-quality rubber seals. With extensive expertise in custom rubber molding, Qualiform excels at solving complex sealing challenges. We offer a wide range of commercial and specification-grade elastomers to manufacture durable, reliable rubber components, including:
- Rubber Gaskets
- Rubber Seals
- Rubber Washers
Qualiform’s experienced team can help you create the high-quality custom rubber products you need. Our technical staff takes multiple factors into account during the design process, enabling them to recommend the best method to meet your quality and cost requirements. Additionally, they can develop new designs if necessary.
There are two separate stages in the life of a gasket or seal:
- The part’s primary fit and function.
- How well the part can endure its environment.
As a result, Qualiform’s experts consider both factors in the design stage of rubber gaskets, so they will not be the weakest link in a product. Similarly, the consider environmental factors in gasket or seal application, such as
- Flammability – UL specifications, heat resistance
- Function – the motion acting upon it
- Impermeability – exposure to gases
- Organic materials needs – fungus resistance, odor, tastelessness
- Temperature extremes – heat, cold
- Weather exposure – water, ozone, sunlight
Whether you need large or small runs, our manufacturing capabilities mean a prompt response to your sealing needs.
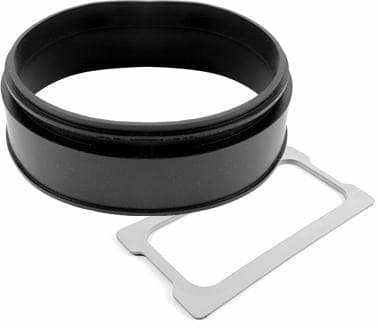
Our technical staff is ready to assist you with all your custom rubber gasket and seal production needs.
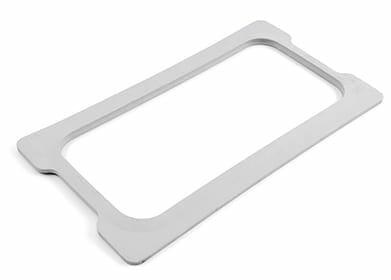
Gray seal created by transfer molding process.
Static Rubber Seals
Where there is little or no motion of assembly parts on the seal.
An initial compression or intervallic compression (open and close) characterizes this type of seal:
- A liquid seal in a hose joint
- A door seal on a home
With the use of a Static Seal, compression pressure operates in a vertical direction relative to the face of an O-ring or face gasket and constricts two different surfaces to eliminate gaps.
Dynamic Rubber Seals
Where there is repetitive motion of assembly parts on the seal.
Repeated actions on the seal, recurrent or intermittent, characterizes this type of seal:
- shock absorption device
- piston ring seal
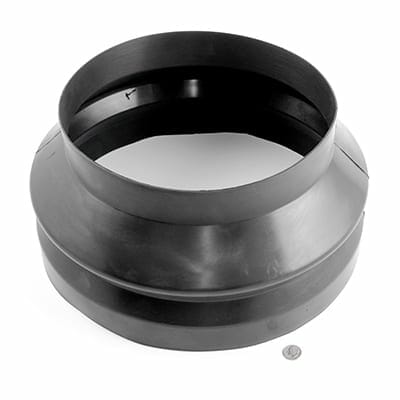
Compression molded viton rubber seal.
Dynamic Seals are more complex than static seals because of the varying stress levels. In addition to Static Seal considerations, Qualiform engineers assess abrasion resistance because it is affected by the companion surface finishes. Other considerations include compression set, temperature changes, thermal cycling, distortion, recovery speed after compression, physical strength, tensile strength, and tear resistance. Qualiform engineers assess all of these environmental forces and provide the most efficient and cost-effective methods to meet our customers’ quality and cost requirements.
Custom Rubber Seals
Custom rubber seals are an essential component in a wide range of applications, offering a tailored solution that ensures superior sealing and protection. Whether you’re dealing with extreme weather conditions, fluctuating temperatures, or exposure to chemicals, custom rubber seals provide unmatched durability and reliability. Qualiform’s custom molded rubber seals are crafted with precision to meet the specific requirements of your equipment, ensuring optimal performance and longevity. With a variety of rubber materials and advanced manufacturing methods, we deliver high-quality custom seals that excel in even the most demanding environments.
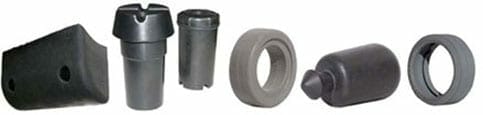
Why Qualiform Rubber Molding?
With 50 years of experience, Qualiform Rubber Molding provides quality rubber products and excellent molding services to its’ customers. We are able to meet the needs created by various industries including industrial, plumbing, aerospace, medical, and electrical. We’ve built a national reputation in the rubber molding business by manufacturing top-of-the-line rubber products.
Qualiform uses special compounds and unique design techniques to solve difficult molding challenges. Our team efficiently finds the best solutions to guarantee customer satisfaction. We put our customers first, therefore, we know how valuable a fast turnaround is. The fastest possible turnaround is provided by an around-the-clock, 24-hour/3-shift workforce.
Qualiform is a certified ISO 9001:2015 company. Through this quality assurance program, we are able to produce top-quality custom rubber molded products. We evaluate your project requirements and ensure that each step of production meets your approval. We are dedicated to implementing an effective quality assurance program that oversees, evaluates, and documents every aspect of our process. This allows us to certify that every product and service we offer is up to top-notch standards.
Qualiform is committed to providing competitive pricing for our customers. We determine pricing based on our evaluation of what is required to make the part. By this analysis, our employees are able to provide our customers with the best solution at the most cost-effective price.
Here at Qualiform, the environment doesn’t take a back seat. We maintain sustainability by using repurposed rubber as frequently as possible. Not only does this reduce our landfill waste input, but it even reduces our material costs.
Qualiform is a top American-owned company in the rubber molding business. All of our tooling is sourced in the United States which allows faster-lead times and faster responses to any design changes.
Our talented team provides full-service manufacturing through our variety of products and services offered.
Types of Customer Rubber Gaskets and Seals We Manufacture
Rubber Transfer Molding FAQ’s
Our Capabilities
Qualiform has the experience and the knowledge to complete your custom rubber molding project needs. In business since 1976, Qualiform has built its enviable reputation on superior quality and a solid commitment to customer service. We have an extensive line of rubber molding services including rubber compression molding, rubber transfer molding, rubber injection molding, and more! Our range of capabilities means we are positioned to provide the custom molded rubber products you require.
From Design through Inspection
From start to finish, Qualiform will produce your design with top-notch customer service. We create quality custom transfer molding, rubber to metal bonding, custom injection molding, and rubber compression molding. We have the ability to complete jobs other manufacturers would fall short in, due to our extensive manufacturing capabilities.
Our Specialties
Our services include custom rubber transfer molding, custom rubber injection molding, rubber to metal bonding, rubber parts manufacturer, custom rubber molding, custom rubber compression molding, rubber parts manufacturer, rubber products manufacturer.
Other Questions?
Qualiform’s customer service is here to offer trustworthy and conscientious communication. Our technical staff will follow up with you all on the details of your order and answer any questions that you may have.
Call us at (330) 336-6777 or submit an inquiry through our contact form.