Is your team looking for a rubber extrusion company for your next project? Qualiform Rubber Molding is a fully-certified industry leader in rubber extrusion, offering a comprehensive range of custom rubber molding services. With our expert staff and state-of-the-art equipment, we ensure the highest levels of quality and precision for every custom rubber molding project, allowing us to develop solutions for virtually any application.
For over 50 years, Qualiform Rubber Molding has been a leading provider of rubber extrusions, supplying high-quality products to a diverse range of industries. Our extensive experience has honed our expertise in all areas of rubber molding, enabling us to complete even the most challenging projects. We excel at creating parts with complex geometries while meeting strict performance standards. Here are some advantages of choosing our rubber extrusion services:
- Ability to create various unique shapes
- Efficient and cost-effective production
- Lightweight, durable products
- Low waste production
In addition, we offer quick lead times, timely delivery, and competitive pricing, so we can create the parts you need at a price you can afford.
Unsure if rubber extrusion is the right choice for your next project? Learn more about our extrusion process below or contact us today to discuss your project with rubber molding experts!
Applications for Rubber Extrusion
A central advantage of using rubber extrusions is their unique versatility. In fact, rubber extrusions are used in a diverse range of industries such as automotive, marine, transportation, healthcare, electronics, food processing, and even aerospace! Here at Qualiform, we offer the expertise necessary for creating the highest quality rubber extrusions on the market regardless of the application.
With our 40+ years of experience in the rubber molding industry, Qualiform Rubber Molding prioritizes quality at every step of the rubber extrusion process. We will work with you to develop a full understanding of your project and provide design and material recommendations. As a result, we can ensure your rubber parts will perform optimally in your application environment. For example, our team will choose materials that offer the best sealing, insulation, wear resistance, or impact and sound absorption to achieve higher levels of performance.
Our state-of-the-art rubber extruders are capable of creating products with a full range of geometries. In fact, rubber extrusions can be found in many typical household items including rubber trim, weather-stripping, rubber floor matting, rubber seals, rubber grommets, and even pencil erasers. Rubber extrusions are particularly useful as seals and gaskets, as they offer incredible impermeability, flexibility, and resistance.
Rubber extrusions can also be found in applications outside the home. They are often used in the manufacturing of cars and bicycles as well as more advanced vehicles such as submarines and space shuttles. Furthermore, many warehouses and manufacturing facilities use rubber extrusions in rubber rollers, sheets, and rods for their exceptional noise and vibration absorption.
Rubber Gaskets and Seals
Extruded rubber gaskets and seals are a Qualiform specialty. Gaskets and seals are designed to keep air and moisture from leaking, so they are useful in a wide variety of industries. We design our rubber gaskets and seals to offer superior resistance in even the most extreme conditions. In fact, we offer a complete selection of commercial and specification grade elastomers to ensure the best performance in any application.
Rubber Window Glazing Seals
Another common form of rubber extrusions is window glazing seals. These seals are designed to insulate windows and prevent air and water from breaching through. As a result, they are commonly used in residential and commercial properties to reduce energy usage. As a leading provider of rubber extrusions, Qualiform can custom manufacture window glazing seals and glazing bead profiles in a full range of rubber compounds for virtually any application.
Rubber Profile Extrusion
Qualiform is a leading provider of custom rubber profile extrusion services. Not all rubber extrusions are created equal, and some shapes are more useful in some applications than others. We can manufacture a full range of rubber extrusion profiles to your exact specifications with high-quality elastomers. Whether you need B profile extrusions for marine fendering or T profile gaskets for sealing and insulation, we have you covered.
Rubber U Channel and U Profile Suppliers
Rubber U channels are one of the many extrusion rubber profiles we offer. These profiles offer a variety of sealing and resistance properties, making them applicable in a wide range of industries. Most importantly, we can customize our rubber extrusion process to create rubber U channels in several different shapes, sizes, and configurations to meet your exact specifications.
Our Rubber Extrusion Process
Here at Qualiform, our rubber extrusion process involves soft, unvulcanized rubber. The extrusion process will make these materials even softer and more flexible, so we have to vulcanize the parts to hard the materials before use in their application.
We start the rubber extrusion process by feeding the unvulcanized materials into our extruder. The extruder will then feed the materials into a hopper, which pushes the rubber into a series of flutes in a revolving screw. This revolving screw will push the rubber into a molding die that we have shaped with a cross-section of the end product. Then, we increase temperatures in the mold as the rubber enters the die.
Once the rubber enters the die, the screw applies pressure and forces the rubber through the opening, and the rubber expands depending on the characteristics of the specific compounds. Any swelling and expansion will need plus or minus tolerances on cross-sections.
Vulcanization of Rubber Extrusions
Vulcanization is an important step in the production of rubber extruded components. This is critical to the post-processing of these parts because it improves the strength of the rubber and performance in the chosen application. Our vulcanization process involves curing the rubber with sulfur and a variety of other agents before moving on to splicing, drilling, cutting to size, end joining, power dusting, and other secondary operations.
Vulcanization of rubber materials will also lead to shrinkage or swelling depending on the present compounds. Once we finish the vulcanization process, the resulting part will typically reduce in size at its center more than at the ends.
If you have any questions or concerns during the extrusion or vulcanization process, our staff will be ready to provide any information or professional recommendations to ensure you receive the best parts for your project.
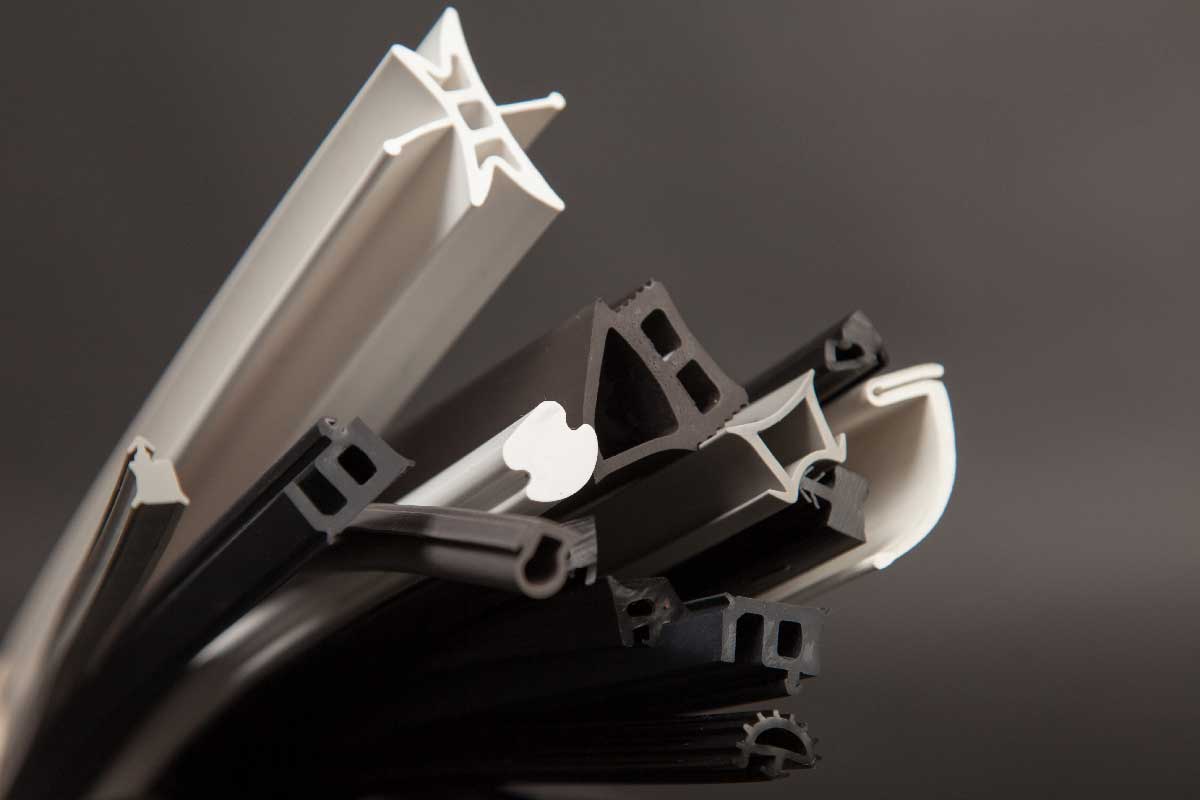
Applications
Glazing Rubber Seals We Produce
Materials Used in Rubber Extruded Products
To create a custom rubber extrusion, rubber extrusion companies think about a number of design factors, all related to the application. One of the first things considered is material. Rubber material choice depends entirely on how it will match the application requirements. Then, our rubber extrusion experts plan out the shape of the die. They may also consult their standard rubber die list, but they make new dies for a custom extrusion.
Based on the required properties and application of the finished extrusion, rubber extrusion company, Qualiform can advise on the best material for the extrusion. Additional consideration will be given to any secondary processes that are required. Custom compounds and fiber integration can be used when needed.
Natural Rubber
Natural rubber provides excellent acid, chemical and abrasion resistance.
Silicone Rubber
Silicone rubber is an FDA-certified elastomer that maintains its form and properties when exposed to both high and low temperatures.
Viton
Viton provides superior heat, chemical and weathering resistance.
Nitrile
Nitrile, aka nitrile rubber, NBR (nitrile butadiene rubber), acrylonitrile butadiene rubber, Perbunan or Buna-Nis, is highly resistant to oils and ideal for O-rings, hoses or hydraulic seals.
Neoprene
Neoprene has high tensile strength and resists heat, fire, UV rays, water and oil.
Butyl
Butyl delivers low air flow permeability.
SBR
SBR (styrene-butadiene rubber) is used in applications that require high abrasion resistance.
EPDM
EPDM (ethylene propylene diene terpolymer) is ideal for applications that involve heat, aging, ozone, oxidation and ultraviolet rays. Can be used for sponge rubber, foam rubber, weather-stripping, tarp straps, door gaskets, window gaskets and roofing membrane.
Benefits of Choosing Rubber Extrusion
There are many reasons to choose rubber extrusion. First, it offers great freedom of design. You can request parts in nearly shape and size, and rubber extrusion companies can use nearly any rubber material. This means that you also have many choices when it comes to the qualities your part will exude. Another great benefit of rubber extrusion is that it makes parts that are both strong and flexible and soft.